Präzise Versuche für einen Präzisionsprozess: Bobcat Company
Anwender
Bobcat Company
Unternehmensinformationen
- Führender Hersteller von kompakten Baumaschinen für Industrie, Landwirtschaft und Bau
- Hauptsitz in West Fargo, North Dakota
- Über 1.000 Bobcat-Händler in 90 Ländern
Herausforderung
Steigerung von Geschwindigkeit und Qualität des Laserschneideverfahrens für Stahlteile
Verwendete Produkte
Minitab® Statistical Software
Ergebnisse
- Produktionsraten des Prozesses wurden um über 20 % verbessert.
- Es wurde eine verbesserte Definition für die Qualität der bearbeiteten Schnittkanten festgelegt.
- Es mussten keine zusätzlichen Lasergeräte angeschafft werden, wodurch über 500.000 US$ eingespart wurden.
- 2.000 Arbeitsstunden mussten nicht extern eingekauft werden.
- Mögliche Einsparungen von insgesamt mehr als 1 Million US$.
Seit über 50 Jahren ist die Bobcat Company weltweit führend in der Entwicklung, der Herstellung und dem Vertrieb von kompakten Baumaschinen, u. a. von Kompaktladern und Kompaktbaggern. Die Baumaschinen von Bobcat werden in unterschiedlichsten Bereichen wie Landwirtschaft, Hoch- und Tiefbau, Landschaftsbau und Geräteverleih eingesetzt. Das Unternehmen verfügt nicht nur über das weltweit umfassendste Vertriebsnetzwerk für kompakte Baumaschinen, es ist auch der größte Produktionsbetrieb in North Dakota. In einem der Werke von Bobcat werden mit Hilfe von Lasern Teile aus großen Stahlblechen geschnitten. Die Kanten dieser Teile müssen glatt sein und dürfen keine Grate oder Krater aufweisen. Das Laserbearbeitungsverfahren führte zu einer akzeptablen Qualität und einem akzeptablen Durchsatz, doch es gab Verbesserungsmöglichkeiten. Darüber hinaus mussten Laserarbeiten an externe Zulieferer ausgelagert werden, obwohl in dem Werk bereits sieben Lasergeräte vorhanden waren. Jim Rose, zertifizierter Master Black Belt bei Bobcat, machte sich daran, dieses Laserbearbeitungsverfahren zu optimieren. Sein Ziel war es, Einstellungen zu bestimmen, mit denen die Geschwindigkeit der Maschinen erhöht und gleichzeitig die Qualität der Teile verbessert werden konnte. Der Erfolg des Projekts war in hohem Maße davon abhängig, dass die Daten effizient erfasst und gründlich analysiert sowie die Ergebnisse richtig interpretiert wurden. Für diese Aufgaben nutzte Rose die Minitab Statistical Software.
Die Herausforderung
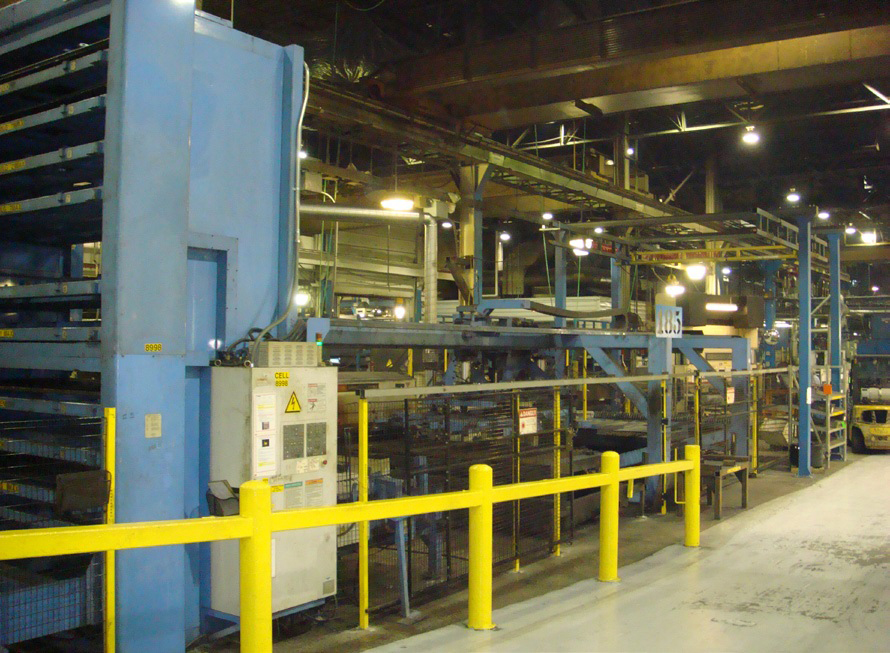
Eine Steigerung des Ertrags von sieben Laserschneidegeräten wie diesem im Bobcat-Werk könnte die Anzahl der extern eingekauften „Laserstunden“ verringern und zu erheblichen Einsparungen führen.
Rose suchte einen „Sweet Spot“, eine optimale Kombination von Werten, die sowohl zu einer schnelleren Laserbearbeitung als auch zu einer besseren Schnittqualität führen würden. Es stand viel auf dem Spiel. Eine Verbesserung der Produktionsgeschwindigkeiten um durchschnittlich 15 % würde die Anschaffung zusätzlicher Laser überflüssig machen, deren Installation jeweils ca. 1 Million US$ kosten würde. Eine Steigerung des Ertrags der sieben vorhandenen Laser würde außerdem die Menge der ausgelagerten „Laserstunden“ reduzieren.
Und da das Werk einen bedeutenden Anteil der Laserarbeiten auslagerte, würde es zu erheblichen Einsparungen führen, wenn auch nur ein Teil dieser Arbeiten wieder vor Ort ausgeführt würde.
Für das Laserschneideverfahren bei Bobcat wurden hohe Schnittgeschwindigkeiten für lange, gerade Schnitte und geringe Schnittgeschwindigkeiten für kurze Schnitte und Winkel eingesetzt. Durch das Ermitteln von Einstellungen, mit denen das Werk eine oder beide dieser beiden Schnittgeschwindigkeiten erhöhen und gleichzeitig die Schnittqualität verbessern würde, könnten die Kapazität des Werks deutlich gesteigert, ausgelagerte Arbeiten wieder ins Werk geholt und Kosten reduziert werden.
Bei der Untersuchung des Verfahrens ermittelte Rose eine Reihe von Faktoren, die Auswirkungen auf die Leistung des Prozesses haben könnten. Hierzu gehörten Leistung (in Watt), der prozentuale Anteil der Schneidezeit, die der Laserstrahl tatsächlich eingeschaltet war (Tastgrad), die Vorschubgeschwindigkeit für die hohe Schneidegeschwindigkeit, die Vorschubgeschwindigkeit für die niedrige Schneidegeschwindigkeit, die verwendete Gasmenge für den Laserbrenner (Hilfsgasdruck), die Weite der Düse zur Steuerung des Strahls und die Fokusdistanz von der Düse zur Schneidefläche. Die Herausforderung bestand nun darin zu bestimmen, welche dieser Faktoren die größten Auswirkungen auf die Leistung hatten, und dann Prozesseinstellungen zu ermitteln, mit denen sowohl die Geschwindigkeit als auch die Produktqualität erhöht werden konnte.
Einsatz von Minitab
Hier kamen die Funktionen für die Versuchsplanung (DOE) der Minitab Statistical Software zum Einsatz. Bei einem Versuchsplan handelt es sich um eine Reihe von Durchläufen oder Tests, bei denen mehrere Variablen angepasst werden. Dies ist ein effektives Verfahren zur Prozessverbesserung, da jeweils mehrere Faktoren geändert und ausgewertet werden können, um anschließend mit Hilfe einer statistischen Analyse aussagekräftige Ergebnisse zu erzielen. Minitab kann Sie dabei unterstützen, die wichtigsten Faktoren zu bestimmen und nachzuvollziehen, welche Wechselwirkungen und Auswirkungen auf den Prozess bestehen. Mit diesem Wissen können Sie die Faktoreinstellungen ermitteln, die zu einer optimalen Prozessleistung führen.
Roses erste Aufgabe bestand darin, die richtige Antwortvariable auszuwählen und zu quantifizieren. Das Verbessern oder zumindest Erhalten der Qualität der mit einer höheren Geschwindigkeit produzierten Teile war ein Hauptziel. Daher wählte er die Schnittqualität als kritische Antwortvariable. Ein Versuchsdurchlauf würde daraus bestehen, ein Stahlblech zu schneiden. Die Schnittqualität würde auf einer Skala von 1–5 bewertet werden, wobei 5 einem perfekten Schnitt entspricht. Zum Festlegen einer Basislinie führte Rose eine vorläufige Analyse der mit den vorhandenen Einstellungen gefertigten Teile durch, die ergab, dass der Prozess zu Schneidevorgängen mit einer durchschnittlichen Bewertung von 4 führte.
Einer der Bediener der Lasergeräte, der bei der Suche nach schnelleren Einstellungen helfen wollte, bot sich zum Bewerten der in den einzelnen Durchläufen produzierten Teile an. Wie jeder Forscher musste Rose vor Beginn des Experiments sicherstellen, dass er sich auf die Genauigkeit des Messsystems verlassen konnte. Er führte mit Minitab eine Prüferübereinstimmung bei attributiven Daten durch, die zeigen sollte, ob der Prüfer die Schnittqualität beständig und genau entsprechend den festgelegten Standards bewerten konnte. Auf der Grundlage der Ergebnisse dieser Analyse wurde einer der Bediener der Lasergeräte als einziger Prüfer ausgewählt. Er konnte sogar ein genaueres Bewertungssystem umsetzen, das mit Werten in Schritten von nur 0,25 anstelle der zuvor verwendeten ganzen Zahlen arbeitete. So wurde die Genauigkeit der erfassten Daten verbessert.
Als die Faktoren, die kritische Antwortvariable und eine zuverlässige Methode für die Datenerfassung gefunden waren, konnte Rose das Experiment planen. Er wusste, dass er bei einem faktoriellen Versuchsplan die Auswirkungen mehrerer Faktoren auf den Prozess untersuchen konnte. Er musste jedoch den Typ des faktoriellen Versuchsplans auswählen, der mit der geringsten Anzahl an Durchläufen zu zuverlässigen Ergebnissen führen würde. Er verwendete Minitab, um die Möglichkeiten zu vergleichen und die beste Option auszuwählen.
Eine Option war ein vollfaktorieller Versuchsplan, ein sehr gründlicher Ansatz, bei dem die Werte der Antwortvariablen bei allen Kombinationen der Faktorstufen erfasst werden. Diese Möglichkeit kann jedoch zu einer unverhältnismäßig hohen Anzahl von Durchläufen führen. Für einen zweistufigen vollfaktoriellen Versuchsplan mit 5 Faktoren sind z. B. 32 Durchläufe erforderlich. Da der Versuchsleiter möglicherweise später Replikationen hinzufügen oder die Durchläufe mehrfach wiederholen möchte, ist ein vollfaktorielles Experiment in vielen Fällen nicht durchführbar.
Rose zog stattdessen teilfaktorielle Versuchspläne in Betracht, bei denen die Anzahl der Durchläufe durch Ausschließen einiger Kombinationen von Faktorstufen auf einen praktikablen Wert reduziert, gleichzeitig jedoch eine zuverlässige Analyse der Faktoren erreicht wird. Bei den Durchläufen handelt es sich um eine ausgewählte Teilmenge oder Fraktion des vollfaktoriellen Versuchsplans. Wenn jedoch nicht alle Faktorstufenkombinationen geprüft werden, bedeutet dies, dass einige Effekte vermengt werden und nicht getrennt voneinander geschätzt werden können. Um aussagekräftige Ergebnisse zu erhalten, muss die Fraktion daher sorgfältig gewählt werden. Zur Vereinfachung des Vorgangs wird in Minitab eine Aliastabelle angezeigt, in der die Muster der vermengten Faktoren angegeben sind.
Für sein erstes Experiment erstellte Rose mit Minitab einen Versuchsplan mit ½-Fraktion, für den nur 16 Durchläufe erforderlich waren (Abbildung 1), mit dem er jedoch trotzdem die Effekte der Faktoren sowie ihrer Zwei-Faktor-Wechselwirkungen schätzen konnte. Rose replizierte die 16 Durchläufe außerdem drei Mal, um die Genauigkeit der erfassten Daten zu verbessern und so die Wahrscheinlichkeit zu steigern, dass mit dem Experiment eine signifikante Differenz ermittelt werden würde.
Mit den Werkzeugen für die Versuchsplanung in der Minitab Statistical Software können Versuchspläne bequem ausgewählt und eingerichtet sowie deren Ergebnisse analysiert werden.
In diesem ersten Experiment wurde festgestellt, dass die Vorschubgeschwindigkeit für die hohe Schneidegeschwindigkeit gefolgt von der Vorschubgeschwindigkeit für die niedrige Schneidegeschwindigkeit die wichtigsten bestimmenden Faktoren für die Prozessgeschwindigkeit waren, und – noch wichtiger – es wurde gezeigt, dass höhere Vorschubgeschwindigkeiten umsetzbar waren (Abbildung 2).
In einem Pareto-Diagramm können Benutzer deutlich die Haupteffekte und Wechselwirkungen erkennen, die die rote Linie kreuzen und daher statistisch relevant sind. Das Diagramm oben zeigt, dass sowohl die Spannung (B) als auch die Wechselwirkung zwischen der Spannung und der Dauer (BC) signifikante p-Werte aufweisen.
Roses erstes Experiment zeigte, dass die Vorschubgeschwindigkeiten bei hoher und niedriger Schneidegeschwindigkeit die wichtigsten bestimmenden Faktoren für die Gesamt-Prozessgeschwindigkeit waren. Ausgehend von diesen Informationen plante er Folgeexperimente, um die Prozesseinstellungen für die Qualität der Teile bei höheren Geschwindigkeiten zu optimieren.
In den nachfolgenden Experimenten konzentrierte sich Rose darauf, die optimalen Einstellungen für die verbleibenden drei signifikanten Faktoren zu finden, um so die Schnittqualität bei der höheren Geschwindigkeit zu verbessern. Ein Würfeldiagramm der Ergebnisse bei erhöhter Geschwindigkeit (Abbildung 3) zeigte die höchste Qualität der Schnittfläche bei geringem Hilfsgasdruck, niedrigem Tastgrad und einem hohem Wert für den Düsenfokus. Außerdem zeigte es, dass die erwartete Schnittqualität höher als der Standard von 4,0 mit den alten Einstellungen war.
Ein Würfeldiagramm zeigte die höchste Schnittqualität bei geringem Hilfsgasdruck, niedrigem Tastgrad und einem hohen Wert für den Düsenfokus, wobei die erwartete Schnittqualität über dem Standard von 4,0 mit den alten Einstellungen lag.
Ergebnisse
Die drei Versuchspläne, mit denen Rose den Laserschneideprozess auswertete, lieferten hervorragende Ergebnisse. Mit den Experimenten wurde eine verbesserte Definition für die Qualität der maschinell bearbeiteten Kanten festgelegt, und es wurden optimierte Einstellungen ermittelt, mit denen die Produktionsraten des Prozesses bei allen Produkten um mehr als 20 % verbessert werden konnten. Aufgrund der Steigerung beim Ertrag der vorhandenen 7 Lasergeräte mussten keine zusätzlichen Laser beschafft werden, wodurch über 500.000 US$ eingespart wurden. Durch die Steigerung entfielen außerdem rund 2.000 „Laserstunden“, die sonst extern eingekauft worden wären. Insgesamt konnten dank der Ergebnisse der von Rose mit der Minitab Statistical Software geplanten und analysierten Experimente mögliche Einsparungen von über 1.000.000 US$ erreicht werden.