Weniger Ausschuss, Nachbesserungen und Kosten bei Tenneco dank der Six Sigma-Methodologie
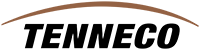
Anwender
Tenneco
Unternehmensinformationen
- Weltweit aktiver Anbieter von Abgasregelsystemen und Fahrwerkprodukten für PKW, LKW sowie andere Nutz- und landwirtschaftliche Fahrzeuge
- Betreibt 90 Werke und 14 Forschungs- und Entwicklungszentren auf sechs Kontinenten
- Ca. 29.000 Mitarbeiter weltweit
- Jahresumsatz von über 8,4 Milliarden US$
Herausforderung
Reduzieren der Ausschussrate für 2,5-Zoll-Rohre um 50 Prozent im Tenneco-Werk in Litchfield, Michigan
Verwendete Produkte
Minitab® Statistical Software
Ergebnisse
- Reduzierung der Ausschussrate für 2,5-Zoll-Stahlrohre um 50 Prozent
- Steigerung der Effizienz in den Abteilungen für interne und externe Kunden
- Umsetzung der Verbesserungen in anderen Werken
Tenneco stellt Abgasregelsysteme und Fahrwerkprodukte für PKW, LKW sowie andere Nutz- und landwirtschaftliche Fahrzeuge für Kunden in über 100 Ländern her. Das Unternehmen betreibt weltweit 14 Forschungs- und Entwicklungszentren und 90 Produktionsstätten und verfügt über ein globales Process-Excellence-Programm, mit dem das Unternehmen Ziele für die kontinuierliche Verbesserung erreicht und Innovation fördert.
„An unseren Produktionsstandorten werde hochwertige Produkte und Systeme mit modernsten Fertigungsverfahren und fortschrittlichen Optimierungswerkzeugen hergestellt“, erläutert Dan Wolfe, Lean Six Sigma Master Black Belt und Master Black Belt Manager für Nordamerika bei Tenneco. „Tenneco setzt die Six Sigma-Methodik und Lean-Verfahren in großem Umfang ein, um ein einheitliches Qualitätsniveau für die Kunden sicherzustellen und die Effizienz an allen Unternehmensstandorten zu verbessern.“
Im Rahmen einer Six Sigma-Initiative zum Reduzieren von Ausschuss und Nachbesserungen bewertete und optimierte ein Team am Standort Litchfield in Michigan in den USA die Prozesse für die Fertigung von Stahlrohren für Abgassysteme in Fahrzeugen.
Das Six Sigma-Projektteam bei Tenneco analysierte mit Minitab Daten und konnte so die Ausschussraten für Stahlrohre verringern, die in Abgassystemen für Fahrzeuge eingesetzt werden.
Die Herausforderung
Im Tenneco-Werk in Litchfield werden Stahlrohre für Abgassysteme in unterschiedlichen Größen hergestellt. Bei den 2,5-Zoll-Rohren trat jedoch die höchste Rate an „Ausschuss“ oder Fehlern auf. Rohre, die als Ausschuss eingestuft wurden, rissen typischerweise während des Fertigungsprozesses an den Nähten oder Bördelungen oder während des Ablängens. Das Projektteam, zu dem auch ein Master Black Belt und Black Belt von Tenneco, Prozessverantwortliche und Ingenieure gehörten, legte als Ziel fest, die Ausschussrate für 2,5-Zoll-Rohre um 50 Prozent zu reduzieren.
Einsatz von Minitab
Das Tenneco-Team arbeitete bei diesem Six Sigma-Projekt mit dem DMAIC-Ansatz, mit dem das Projekt in fünf Phasen unterteilt wurde: Definieren, Messen, Analysieren, Verbessern und Kontrollieren. (Das Akronym DMAIC leitet sich von den englischen Bezeichnungen Define, Measure, Analyze, Improve und Control ab.) In der Definitionsphase erstellte das Team detaillierte Process Maps, mit denen die Schritte beim Fertigen von Abgasrohren dargestellt wurden. Es wurde sogar ein externer Lieferant hinzugezogen, um detaillierte Informationen zu einigen der technischeren Aspekte des Prozesses zu erhalten und so Verbesserungsmöglichkeiten aufzuzeigen.
Zur weiteren Auswertung des derzeitigen Prozesses führte das Team in Minitab eine Prozessfähigkeitsanalyse mit den Daten zu der Anzahl von Fehlern durch. Die Analyse zeigte dem Team, dass der Anteil von Fehlern relativ variabel war, wobei die durchschnittliche Fehlerrate bei 1,32 Prozent lag.
Das Projektteam bei Tenneco führte zu Beginn des Projekts eine Prozessfähigkeitsanalyse in Minitab durch, um die Prozessstreuung zu untersuchen.
Nachdem nun mehr Informationen zu dem Prozess vorlagen, legte das Team eine Rangfolge für Bereiche fest, in denen Verbesserungen möglich waren. Hierzu zählten Abnutzung und Ausrichtung von Werkzeugen, Temperatur im Schweißbereich, Werkzeugeinrichtung, Druck und Überprüfung. Das Team erfasste dann Daten für jede dieser potenziellen Verbesserungsmöglichkeiten, z. B. stetige Temperaturdaten aus dem Schweißprozess, und bereitete die statistische Analyse vor, um die Bereiche zu ermitteln, auf die sie sich zum Reduzieren der Ausschussraten konzentrieren sollten.
Mit Minitab wurden verschiedene Hypothesentests durchgeführt, u. a. Tests von Anteilen bei zwei Stichproben, um zu beurteilen, ob neue Werkzeuge die Ausschussraten beeinflussen würden oder ob die Nutzung der vom Hersteller empfohlenen Einstellungen für die Werkzeugeinrichtung Auswirkungen hätte.
Außerdem untersuchte das Team mit einer Varianzanalyse (ANOVA) in Minitab die Auswirkung der Temperatur im Schweißbereich auf die Ausdehnung der Rohre, da ausgedehnte Rohe anfälliger für Fehler sind. Mit einer solchen Analyse wird die Bedeutung eines oder mehrerer Faktoren durch Vergleich der Mittelwerte der Antwortvariablen bei den unterschiedlichen Faktorstufen ausgewertet. In diesem Fall waren die unterschiedlichen Faktorstufen die verschiedenen Temperaturen (1500 °F, 1700 °F, 1850 °F, 1950 °F).
Das Team führte in Minitab einen Test von Anteilen bei zwei Stichproben durch (oben links), um zu untersuchen, ob die Verwendung der vom Hersteller empfohlenen Einstellungen für die Werkzeugeinrichtung Auswirkungen auf die Ausschussraten hat. Außerdem wurde mit einer ANOVA (unten rechts) analysiert, welche Auswirkungen unterschiedliche Temperaturen im Schweißbereich auf Fehler im Zusammenhang mit der Ausdehnung der Rohre haben.
„Die Minitab-Analyse bestätigte, dass wir unsere Arbeit auf Verbesserungen bei den Werkzeugen konzentrieren und die Verfahren für die Werkzeugeinrichtung sowie die Temperaturen für den Schweißbereich standardisieren sollten“, berichtet Peter Malefyt, Senior Engineer und Black Belt am Tenneco-Standort Litchfield. „Dies ist nur ein Beispiel dafür, wie wir mit Minitab Daten analysieren und Lösungen für die Prozessverbesserung entwickeln.“
Das Team untersuchte diese Verbesserungsmöglichkeiten in kleinen Produktionsdurchläufen. Mit Boxplots und Regelkarten in Minitab konnte das Team leicht die Ergebnisse der Testläufe erkennen. Eine Messsystemanalyse zeigte, dass das Team sich auf die erfassten Daten verlassen konnte. Die Analyse der Daten aus den Testläufen bestätigte die Verbesserungsmöglichkeiten, die bereits vorher ermittelt worden waren.
Mit Boxplots und Regelkarten in Minitab konnte das Projektteam die Daten aus den Testproduktionsläufen analysieren und die Verbesserungsmöglichkeiten anhand übersichtlicher Darstellungen der Daten validieren.
„Mit Minitab-Grafiken können wir komplexe statistische Ergebnisse leicht verständlich für alle in unserer Organisation kommunizieren“, bestätigt Malefyt.
„Die Dokumentation und integrierte Hilfe für die Minitab Statistical Software sind besser als alles, was wir bei Tenneco verwendet haben, und unterstützen uns auch bei der Schulung enorm“, ergänzt Wolfe.
Nachdem bekannt war, an welchen Stellen Verbesserungen benötigt wurden, setzte das Team Lösungen um, mit denen das Ziel für die Reduzierung des Ausschusses am wahrscheinlichsten erfüllt werden konnte. Die Kosten für die Umsetzung wurden anhand von Kosten-Nutzen-Analysen gerechtfertigt. Zu den Lösungen gehörten die Einführung eines neuen Messsystems und Steuerungen für die Werkzeuge, das Festlegen von Temperaturparametern sowie die Standardisierung der Bedingungen für die Werkzeugeinrichtung.
Ergebnisse
Die Ergebnisse einer Analyse der Daten, die nach der Umsetzung der Prozessverbesserungen erfasst wurden, bestätigten, dass das Team das Ziel erreicht hatte, den Ausschuss um 50 % zu reduzieren.
Das Projektteam erstellte eine Regelkarte mit Abschnitten (oben), um dem Management die Veränderung des Prozesses während der Umsetzung der Verbesserungen zu veranschaulichen. Das Team konnte drei Zeitabschnitte – der Prozess vor der Verbesserung (Basisdaten), die anfänglich entwickelte Lösung (verbessert) und die optimierte Lösung – gemeinsam auf einer Regelkarte darstellen.
Zudem wurden Verbesserungen der Effizienz bei den Abteilungen für interne und externe Kunden erreicht, die die Stahlrohrteile im Werk in Litchfield fertigen.
Im Boxplot oben werden die Gesamtproduktivität vor und nach der Umsetzung der Verbesserungslösungen für die Abteilungen gezeigt, die die 2,5-Zoll-Stahlrohre fertigen.
Das Projektteam hat seinen Erfolg den Verbesserungsteams an anderen Tenneco-Standorten mitgeteilt, die Teile in anderen Größen fertigen oder in denen ähnliche Produktionsverfahren eingesetzt werden.
„Deswegen sind die Auswirkungen dieses Projekts so viel umfassender, als die Zahlen zeigen“, erläutert Malefyt. „Tenneco fertigt Stahlrohre in vielen unterschiedlichen Größen, und diese Verbesserungen können bei allen diesen Prozessen in allen unseren Werken umgesetzt werden.“
Die Teammitglieder ergänzen, dass ihr Projekt nur eines einer Vielzahl von erfolgreichen Projekten ist, die jedes Jahr im Rahmen des globalen Process-Excellence-Programms von Tenneco durchgeführt werden.
„Minitab ist integraler Bestandteil unserer Six Sigma-Schulung und integraler Bestandteil von erfolgreichen DMAIC-Projekten bei Tenneco“, fasst Wolfe zusammen.